Our Technology
Phase Two Chemicals is revolutionizing electrochemistry with our proprietary Phase Dispersion Electrode (PDE). Our advanced stack was co-developed with the PDE, maximizing efficiency of the process. By enabling lower-cost, on-site production of this essential chemical, we enhance reliability, reduce supply chain dependencies, and promote more sustainable bleaching processes.
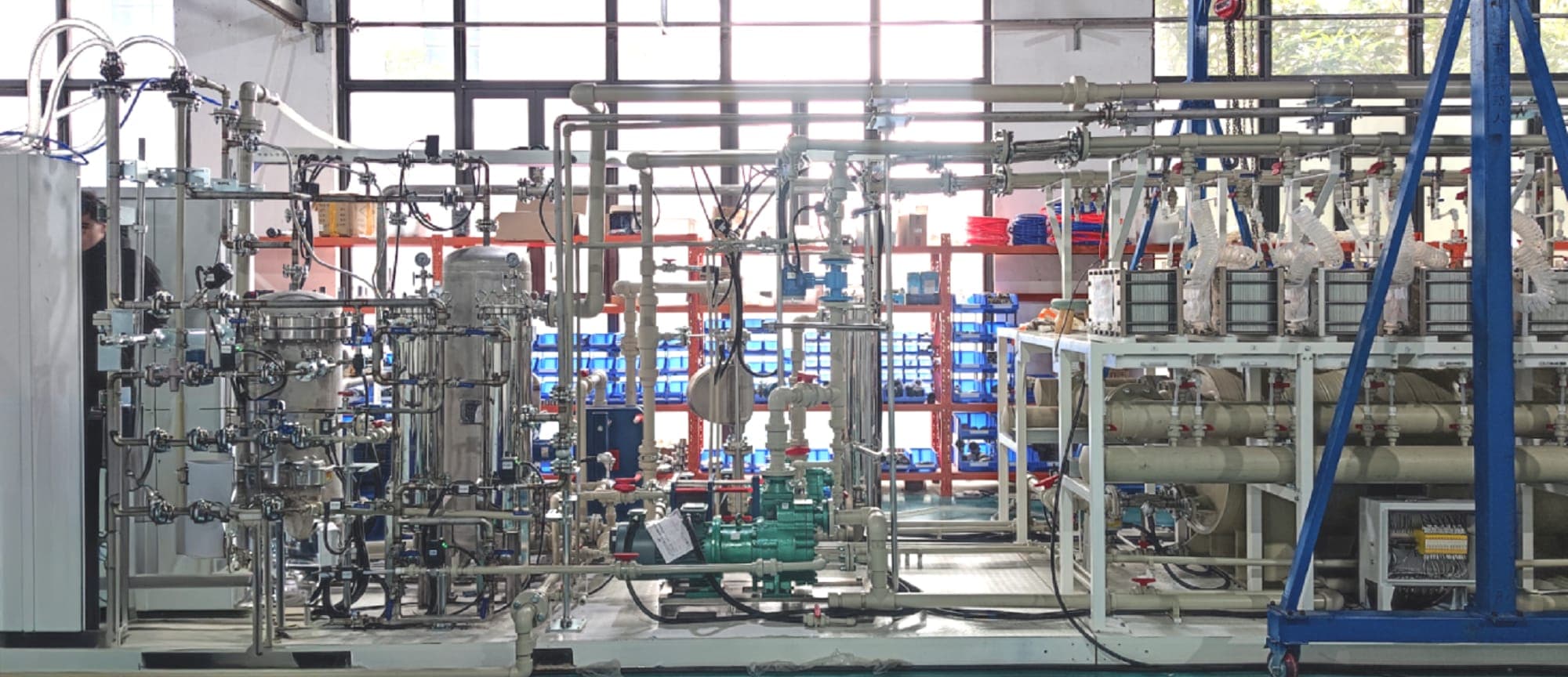
Revolutionizing Chemical Production
Leading the Charge for Green Chemical Production
At Phase Two Chemicals, we're at the forefront of the clean chemistry revolution, pioneering on-site hydrogen peroxide production through our groundbreaking electrolytic synthesis technology. We're not just changing the way hydrogen peroxide is produced; we're setting a new standard for the chemical industry.
Our Technology
Explore the technology and equipment we use to develop and refine electrochemical processes, ensuring reliability, efficiency, and precision in every application.
Innovation in Action
Cutting Edge Technologies
Fueling our revolutionary success is an extensive journey of research and development spearheaded by our visionary founders. Phase Two Chemicals has pushed the envelope in electrocatalysis, electrode design, and stack architecture for multi-phase electrochemical reactions through innovation fueled by grit, perseverance, ingenuity, and a belief that we can do better. This fusion of cutting-edge technologies empowers an exceptionally efficient electrolytic synthesis of hydrogen peroxide, setting us apart as trailblazers in the industry.
Learn About Our Processes →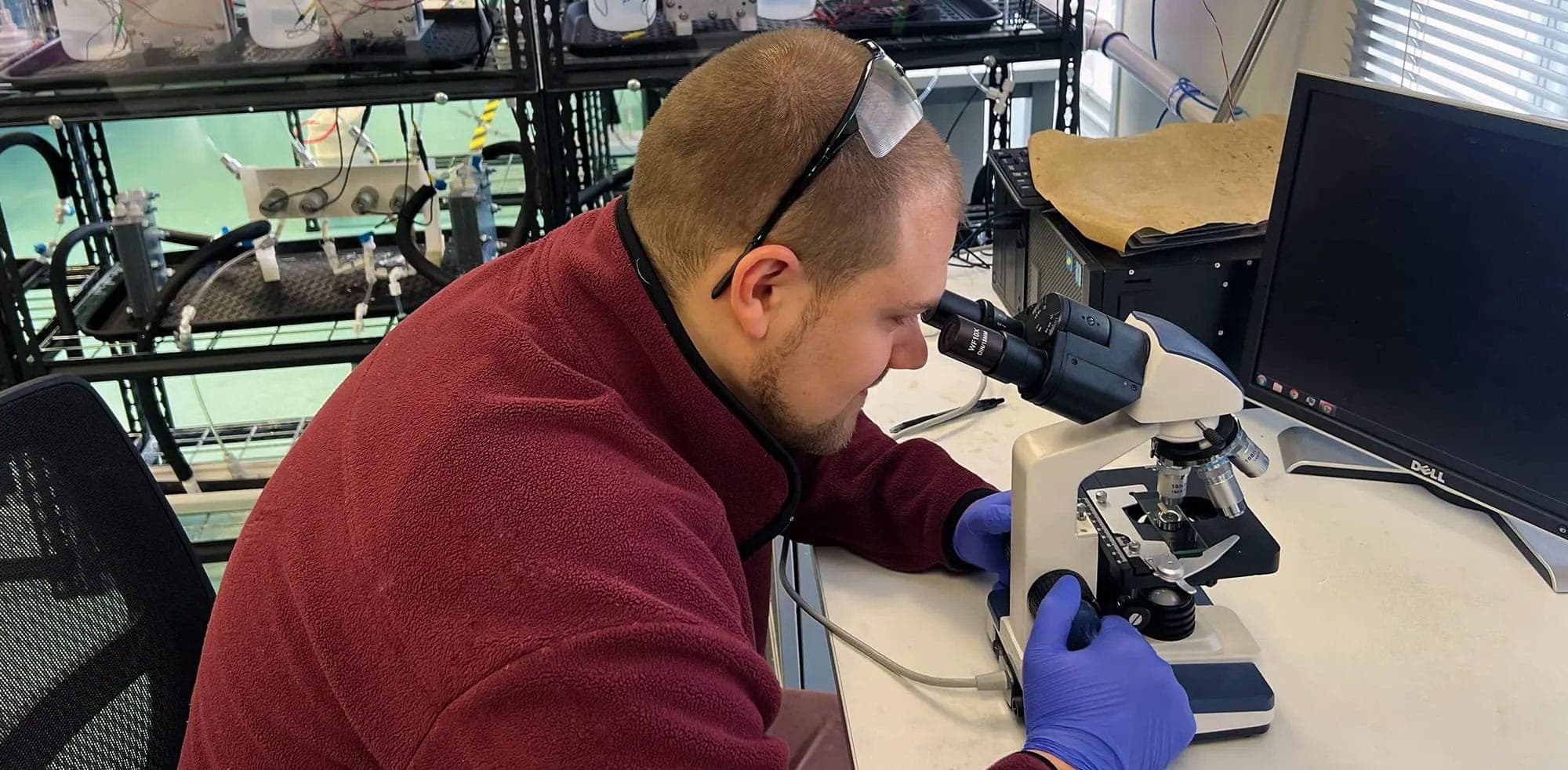
Technology Spotlight
Advanced Phase Dispersion Electrode Technology
Phase Dispersion Electrode (PDE)
Our proprietary PDE technology optimizes gas-liquid reactant delivery to the electrode surface, significantly enhancing the two-phase electrochemical reaction efficiency essential for hydrogen peroxide generation.
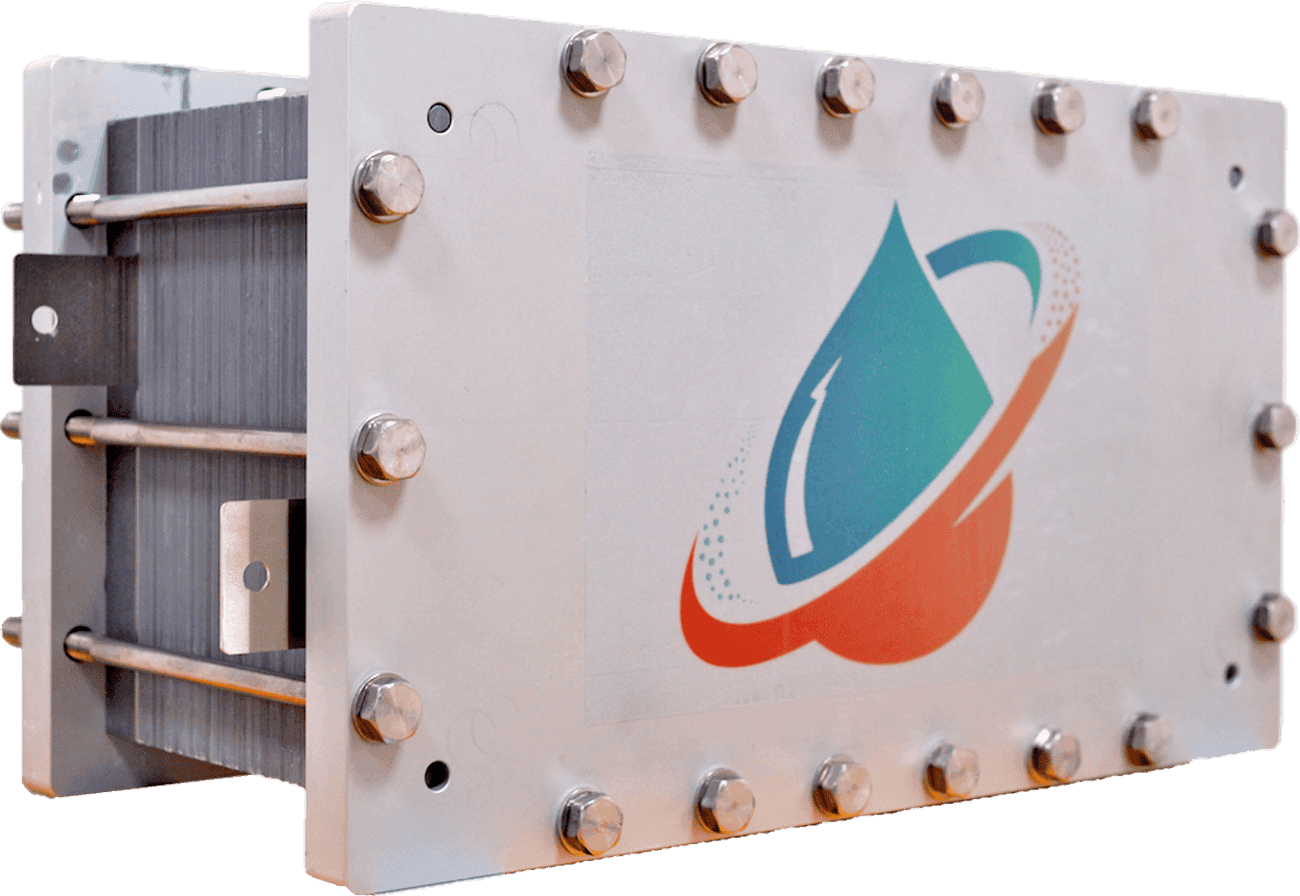
Miniaturization and Energy Efficiency
The innovative stack design allows for a compact system footprint while maximizing energy efficiency, achieving superior performance compared to prior attempts at commercialized electrosynthesis of hydrogen peroxide.
Electrochemical Stack Design
The stack features next-generation electrodes, meticulously designed and fabricated using advanced manufacturing techniques for optimal performance.
Operational Excellence
Transforming Innovation with Modular, Efficient, and Flexible Solutions
Our system is modular by design. Systems have 50% turndown and have less than 2-hour start-up time, enabling us to match the amount of peroxide demanded without impacting operations or energy efficiency. The system is automated and remotely operable. Experience the power of our modular design—crafted to help your business move faster, smarter, and greener.
Cost-Effective
Reduce the cost of hydrogen peroxide through the efficient one-step electrochemical process and the elimination of transportation costs.
Sustainable
Lower your environmental impact by using the inherently carbon-free electrochemical process and eliminating emissions from transportation.
Security of Supply
On-site production reduces supply chain risk associated with transportation.
Experience the Next Phase in Hydrogen Peroxide Production
Ready to transform your hydrogen peroxide supply chain with cutting-edge electrochemical technology? Contact our technical team to learn how our on-site generation systems can meet your specific needs.
Get in Touch With Our Experts →